Cast vs. Forged Valves: Make the Right Choice for Your System
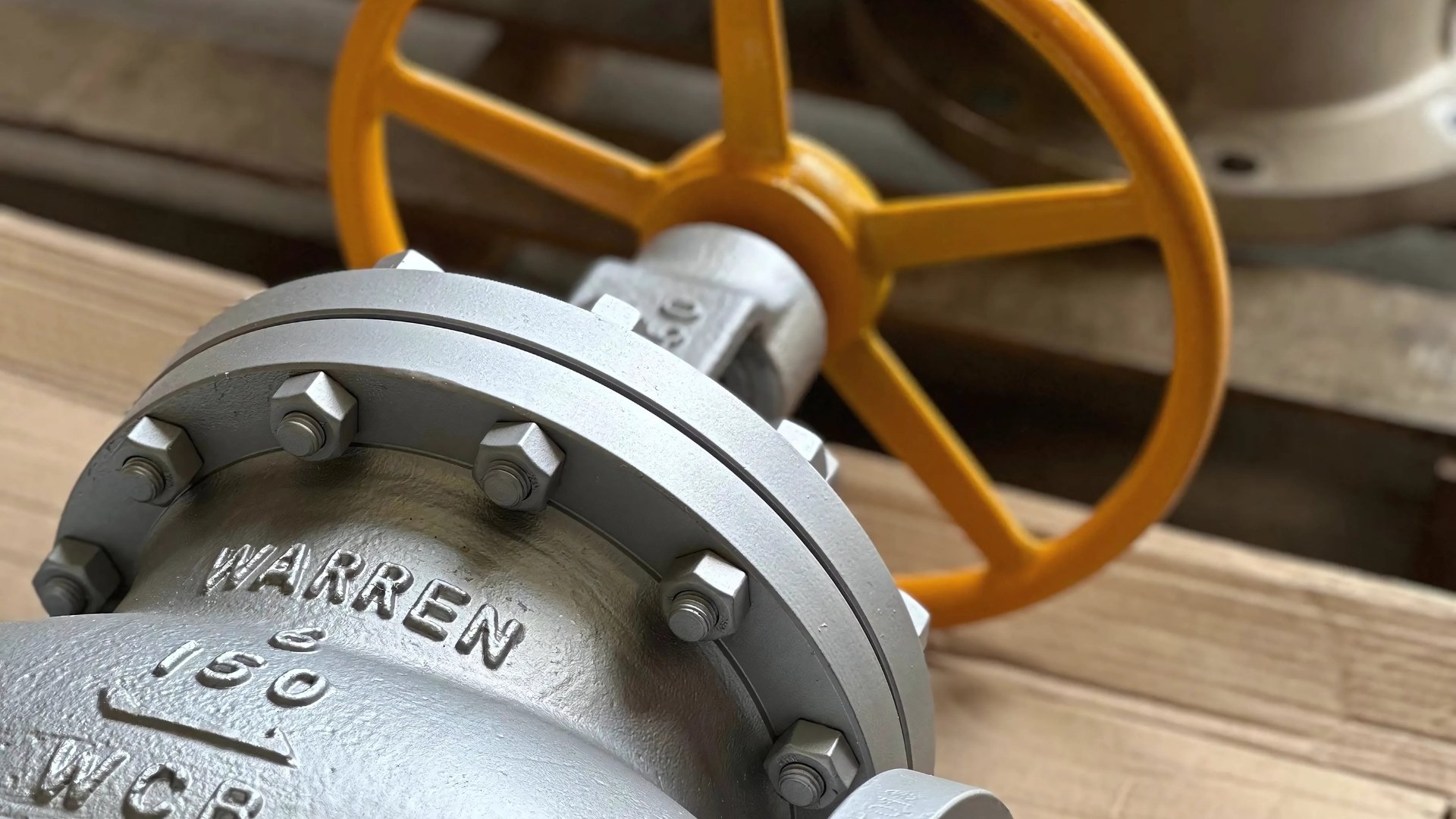
When designing or maintaining industrial systems, valve selection can make or break your operation. Two manufacturing methods dominate the industry: casting and forging. Each brings distinct advantages to the table, and understanding these differences is crucial for making informed decisions. Let’s dive into what makes each method unique and how to choose between them.
Cast Valves: The Art of Melting and Molding
Casting involves transforming metal from liquid to solid form by pouring molten material into specifically designed molds. Once cooled and solidified, the valve emerges from its mold ready for finishing touches.
Key Advantages of Cast Valves
- Economic Efficiency: Casting shines in cost-effectiveness, particularly for large production runs. The reduced machining requirements compared to forged valves translate to significant savings.
- Material Versatility: Need a special alloy? Casting accommodates a wide range of metals and alloys that might be impractical or impossible to forge.
- Design Flexibility: Complex geometric designs are casting’s specialty. Intricate internal passages and complex shapes that would challenge other manufacturing methods are readily achievable.
- Rapid Availability: When downtime threatens production, cast valves offer shorter lead times for replacement parts, keeping operations running smoothly.
Major Casting Techniques
Sand Casting
Sand casting remains the industry workhorse, particularly for steel valve production. The process begins with pressing mold patterns into sand-filled boxes, then removing these patterns to leave precise impressions in the sand. Workers then carefully assemble and secure the sand molds together before pouring molten metal through strategic entry points. After cooling, the cast component is removed from the sand and undergoes surface finishing to meet specifications. While ideal for larger valve components, sand casting typically commands a higher price point than alternative methods.
Investment Casting
For smaller valve components requiring higher accuracy, investment casting (also known as “lost wax” casting) offers an economical solution. The process starts with creating a wax pattern of the desired component, followed by coating the pattern with ceramic slurry. After curing the ceramic, the wax melts out, leaving a precise cavity. The ceramic mold is then heated to approximately 1000°C to remove any residual wax and moisture before pouring molten metal into the cavity. Once cooled, the ceramic is broken away to reveal the finished component. This method typically handles components up to 100 kg with maximum dimensions of 1.6 meters, delivering excellent surface finish and dimensional accuracy.
Forged Valves: Strength Through Pressure
Unlike casting, forging shapes metal while it remains solid. The process applies compressive forces to reshape metal, while specialized dies serve the dual purpose of shaping and cutting the material into specific valve components. Success depends on working between the material’s elasticity and strength limits, making forging particularly suited to ductile materials.
Key Advantages of Forged Valves
- Superior Structural Integrity: The forging process aligns the metal’s grain structure, creating a homogeneous material with enhanced tensile and yield strength, reducing failure risk dramatically.
- Fatigue Resistance: By eliminating internal voids and gas pockets that plague other manufacturing methods, forged valves offer exceptional reliability over extended operational periods.
- Thermal Performance: The thinner walls characteristic of forged valves facilitate faster thermal transfer, allowing quicker heating and cooling. This makes them ideal for systems experiencing frequent startup/shutdown cycles or extreme temperature variations.
Forging Methods
Valve forging techniques fall into two main categories: those distinguished by operating temperature and those categorized by the physical shaping technique employed. When examining temperature-based approaches, manufacturers typically utilize three distinct methods:
- Cold Forging: Performed at room temperature, requiring greater mechanical force but delivering excellent dimensional control and surface finish.
- Warm Forging: Conducted at moderate temperatures (800-1000°C), striking a balance between required force and material malleability.
- Hot Forging: Operating above 1000°C (but below 1300°C), maximizing material ductility and minimizing required forming pressure.
Beyond temperature considerations, valve forging can also be distinguished by the physical techniques used to shape the metal. These process-oriented approaches include:
- Open Die Forging: Versatile method where dies don’t completely enclose the workpiece, suitable for everything from small components to massive pieces. Produces exceptionally durable parts in shapes like discs, rings, and cylinders.
- Closed Die Forging: Precision-focused technique completely enclosing the metal, ideal for producing smaller, complex components with tight tolerances in high volumes.
Making Your Decision: Cast vs. Forged
Selecting between cast and forged valves requires balancing multiple system requirements against each manufacturing method’s inherent strengths. From a financial perspective, casting typically provides cost advantages for complex designs, though the higher initial investment in forged valves often translates to lower lifetime costs through extended durability. The operating environment plays a decisive role as well, with standard pressure systems generally performing well with cast valves, while high-pressure applications benefit from the superior structural integrity of forged alternatives.
Your system’s temperature profile should also influence your decision. Cast valves function adequately in moderate temperature settings, but forged valves truly shine when facing extreme temperature variations, thanks to their uniform grain structure and superior heat transfer properties. System cycling frequency is crucial to take into consideration as cast valves are better suited for steady-state operations, while forged valves handle frequent startup and shutdown cycles more effectively with less thermal fatigue.
The Bottom Line
While cast valves offer cost advantages, design flexibility and faster production timelines that make them popular in many applications, forged valves deliver unmatched strength, durability, and performance in demanding environments. Understanding your system’s unique requirements such as pressure ratings, temperature fluctuations, cycling frequency, and budget constraints, will guide you to the optimal choice for your operation.
Remember that neither manufacturing method is inherently superior; each serves specific purposes within every industry. By matching your application needs to the appropriate manufacturing process, you’ll ensure optimal performance, safety, and operational efficiency.