The Complete Guide to Hydraulic Fittings: Sealing Methods and Applications
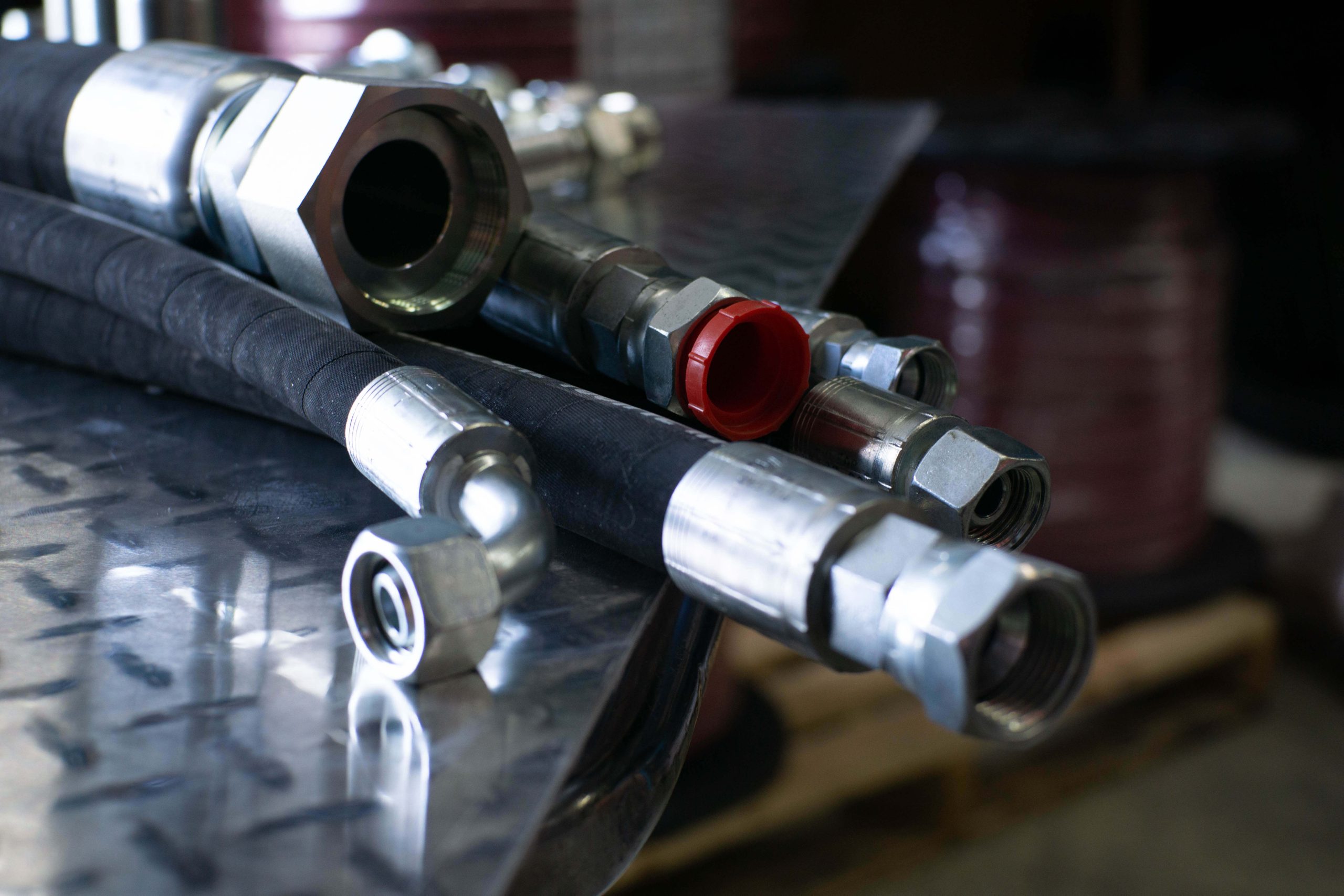
Hydraulic systems power everything from paper mills and steel plants to excavators, tractors, automobiles, and aircrafts, making reliable connections between components critical for efficient fluid power transmission while maintaining system pressure and preventing contamination. Understanding how different fitting types create their seals and where they’re most effective is essential for anyone working with hydraulic equipment across any one of these industries.
JIC (Joint Industry Council) Fittings
JIC fittings utilize a 37° flare seal that creates a metal-to-metal seal between male and female components. When the fittings are tightened, the angled surfaces compress together to form a reliable seal without requiring additional gaskets or o-rings. This design makes JIC fittings ideal for mobile hydraulic applications such as construction equipment, agricultural machinery, and automotive systems where vibration and movement are common. The metal-to-metal seal provides excellent resistance to pressure fluctuations and temperature variations.
ORFS (O-Ring Face Seal) Fittings
ORFS fittings use an o-ring that sits in a groove on the flat face of the male fitting and seals against the corresponding flat face of the female fitting. This face-seal design excels in high-pressure applications and provides superior resistance to vibration-induced loosening compared to tapered thread connections. ORFS fittings are predominant in aerospace applications, high-pressure industrial hydraulics, and precision machinery where leak-free operation is critical.
ORB (O-Ring Boss) Fittings
ORB fittings combine straight threads with an o-ring seal. The male fitting screws into a female port until an o-ring positioned at the base of the male threads compresses into a slight machined chamfer on the female port, creating a leak-free seal. ORB fittings share the same thread specifications as JIC fittings, only differing in their sealing method and application. This standard is extensively used in mobile hydraulic equipment, and industrial applications where space constraints require compact fittings with reliable sealing.
BSP (British Standard Pipe) Fittings
BSP fittings come in two types: parallel threads (BSPP) that require a gasket or o-ring for sealing, and tapered threads (BSPT) that create a seal through interference fit, similar to NPT (National Pipe Thread). BSP fittings dominate hydraulic applications throughout Europe, Asia, and former British Commonwealth countries, and are commonly found in industrial hydraulic systems, marine applications, and process equipment manufactured in these regions.
NPT/NPSM (National Pipe Thread) Fittings
NPT fittings create their seal through tapered thread interference fit, where the male thread compresses into the female thread enhanced with thread sealant or PTFE tape. NPSM threads are straight and require a gasket or o-ring for sealing. NPT fittings are common throughout North American industrial applications, including stationary hydraulic systems, process equipment, and general plumbing applications.
JIS (Japanese Industrial Standard) Fittings
JIS fittings use a 30° flare seal, similar to JIC but with different dimensional specifications. The metal-to-metal contact between flared surfaces creates a reliable seal that withstands high pressures and temperature variations. JIS fittings share the same thread specifications as BSPP fittings but differ in their sealing method, as JIS uses a flared seat while BSPP requires a gasket or o-ring. JIS fittings are predominantly used in hydraulic equipment manufactured in Japan and throughout Asia, including construction machinery from manufacturers like Komatsu, Hitachi, and Kobelco.
Komatsu Fittings
Komatsu fittings represent a proprietary standard developed specifically for Komatsu construction and mining equipment, featuring a 30° flared seat with metric threads. These fittings are engineered for extreme construction and mining environments and are found exclusively on Komatsu equipment including excavators, bulldozers, wheel loaders, and mining trucks.
DIN (German Metric) Fittings
DIN (Deutsches Institut für Normung) fittings utilize a 24° cone seat with both male and female components featuring straight metric threads. The sealing occurs between the 24° seat in the male fitting’s recessed counter bore and the corresponding female component, which can be a metric DIN female fitting, metric tubing with a compression ring and nut, or a 24° cone with an o-ring. DIN fittings are available in three pressure series: LL (Extra Light) for low-pressure applications, L (Light) for medium-pressure applications, and S (Heavy) for high-pressure applications. DIN fittings are predominantly used throughout Europe in automotive brake and fuel systems, marine applications, construction equipment, and industrial machinery where metric-sized tubing and German engineering standards are specified.
Code 61 and Code 62 Fittings
Code 61 and Code 62 fittings are flange connection standards using four bolts to compress a flat gasket or o-ring between matching flange faces. The large sealing surface handles extremely high pressures and flow rates. These flanged connections are used in high-pressure hydraulic applications such as large construction equipment, industrial presses, and power transmission systems where pressures exceed 5,000 PSI.
CAT Style Flange Fittings
CAT style flange fittings represent Caterpillar’s proprietary flange connection system designed for heavy construction and mining equipment. These fittings utilize flat face sealing with an o-ring or gasket compressed between flange faces and share the same bolt pattern as Code 62 flanges, but the flange head remains a consistent 5/8″ thickness regardless of dash-size. They provide exceptional resistance to shock loads, vibration, and pressure spikes while allowing easy disconnection during maintenance.
Conclusion
The diversity of hydraulic fittings reflects the varied demands of different industries and applications, with each design optimized for specific operating conditions. Understanding the sealing mechanisms and appropriate applications for each fitting type is crucial for system reliability, leak-free operation, and optimal equipment performance.